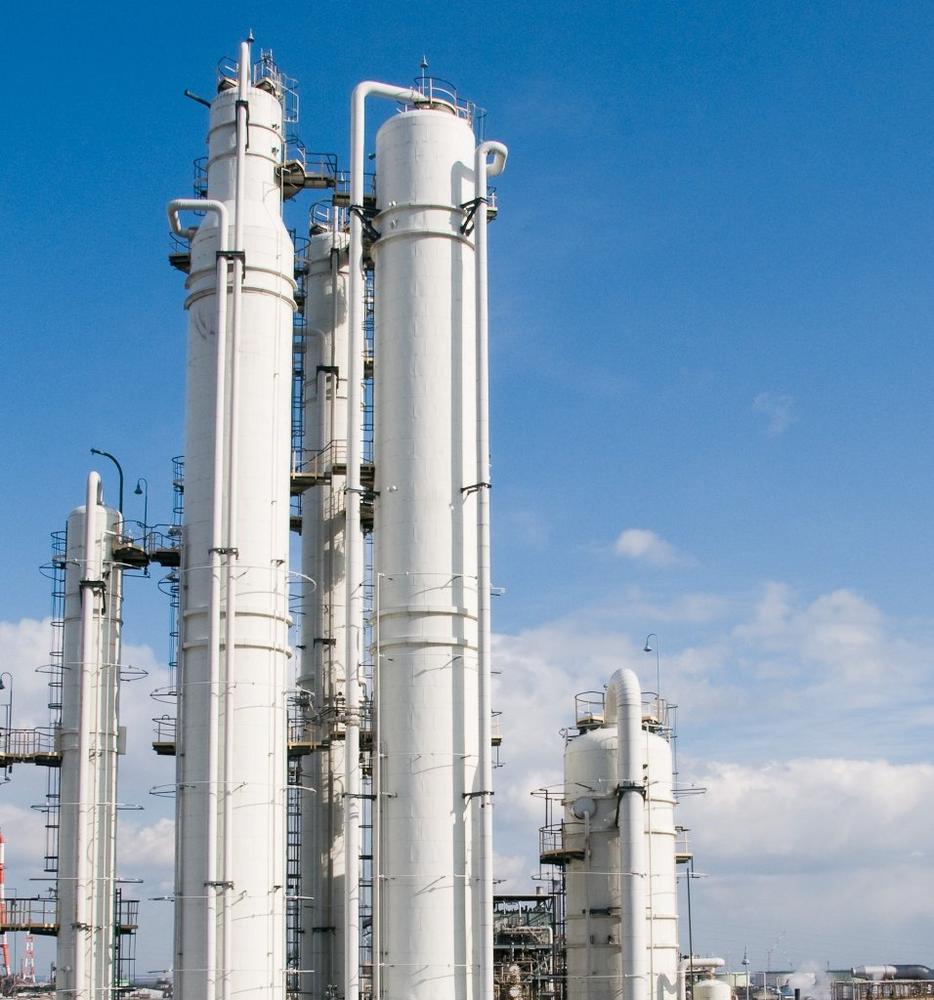
Steuerungen sind in der Prozessindustrie für ein breites Spektrum von Bereichen wichtig: von der Ölraffination und Petrochemie bis hin zu Hochleistungschemikalien, Glasfasern, Stahl, Pharmazeutika, Lebensmitteln und Wasser. All dies beinhaltet chemische Reaktionen und andere Elemente, die einen äußerst hohen Grad an Zuverlässigkeit erfordern.
Im Praxistest konnte die KI-Lösung erfolgreich die komplexen Bedingungen bewältigen, die erforderlich sind, um die Produktqualität zu gewährleisten und den Flüssigkeitsstand in der Destillationskolonne auf einem angemessenen Niveau zu halten, während gleichzeitig Abwärme als Wärmequelle bestmöglich genutzt wurde. Auf diese Weise konnte die Qualität stabilisiert, ein hoher Ertrag erzielt 4 und Energie gespart werden. Regen, Schnee und andere Witterungseinflüsse waren zwar Faktoren, die den Kontrollzustand durch plötzliche Veränderungen der Lufttemperatur stören konnten, aber die hergestellten Produkte entsprachen strengen Normen und wurden inzwischen ausgeliefert. Da nur qualitativ hochwertige Produkte hergestellt wurden, entfielen außerdem Kraftstoff-, Arbeits- und Zeitverluste sowie andere Verluste, die bei der Herstellung von Produkten entstehen, die nicht den Spezifikationen entsprechen. Über ein dreistufiges Verfahren konnte ein sicherer Betrieb gewährleistet werden.
Die bei diesem Kontrollexperiment verwendete KI, das Protokoll „Factorial Kernel Dynamic Policy Programming“ (FKDPP), wurde 2018 gemeinsam von Yokogawa und dem Nara Institute of Science and Technology (NAIST) entwickelt und im Rahmen der International Conference on Automation Science and Engineering des IEEE als weltweit erste KI anerkannt, die für das Anlagenmanagement genutzt werden kann7. Über Initiativen wie die erfolgreiche Durchführung eines Experiments mit einem Steuerungstrainingssystem8 im Jahr 2019 und einem Experiment im April 2020, bei dem eine gesamte Anlage mittels eines Simulators nachgebildet wurde9, konnte Yokogawa das Potenzial dieser KI für autonome Steuerung10 bestätigen und von einer Theorie in eine für die praktische Nutzung geeignete Technologie weiterentwickeln. Diese kann in Bereichen genutzt werden, in denen eine Automatisierung mit herkömmlichen Regelungsmethoden (PID-Regelung und APC) bisher nicht möglich war. Eine der Fähigkeiten dieser Technologie ist es, widersprüchliche Ziele zu bewältigen, wie z. B. der Forderung nach hoher Qualität und Energieeinsparung.
Angesichts der zahlreichen komplexen physischen und chemischen Phänomene, die sich auf den Betrieb von Anlagen auswirken, gibt es weiterhin viele Situationen, in denen erfahrenes Fachpersonal eingreifen und die Kontrolle übernehmen muss. Selbst wenn der Betrieb mittels PID-Regelung und APC automatisiert wird, müssen Fachleute mit viel Erfahrung die automatisierte Steuerung anhalten und Konfiguration und Ausgangswerte ändern, wenn beispielsweise eine plötzliche Veränderung der Lufttemperatur aufgrund von Niederschlägen oder anderen Wetterereignissen auftritt. Dies ist ein verbreitetes Problem, das in vielen Anlagen auftritt. Beim Übergang zur industriellen Autonomie besteht eine große Herausforderung darin, eine autonome Steuerung in Situationen einzuführen, in denen bisher ein manuelles Eingreifen unerlässlich war – und zwar mit so wenig Aufwand wie nötig, bei gleichzeitiger Gewährleistung eines hohen Sicherheitsniveaus.
JSR ist überzeugt, dass diese Demonstration das Potenzial von KI für die Bewältigung von Herausforderungen zeigt, die in Chemiewerken bisher nicht gelöst werden konnten. Das Unternehmen wird die Anwendung von KI bei weiteren Verfahren und in anderen Werken untersuchen, um weitere Produktivitätssteigerungen zu erzielen. In Zukunft werden beide Unternehmen weiterhin zusammenarbeiten und Möglichkeiten untersuchen, wie KI in Anlagen genutzt werden kann.
Masataka Masutani, General Manager Produktionstechnologie bei JSR:
„In einem Umfeld, das sich aufgrund von Faktoren wie der flächendeckenden Einführung von 5G und anderen Entwicklungen hin zu einer digitalen Gesellschaft sowie der Überalterung des Personals, das die Anlagensicherheit gewährleistet, und dem Mangel an Arbeitskräften, die sie ersetzen könnten, verändert, steht die petrochemische Industrie unter starkem Druck, die Sicherheit und Effizienz ihrer Produktionsaktivitäten durch den Einsatz neuer Technologien wie IoT und KI zu verbessern. JSR ist darauf ausgerichtet, die Produktion durch die proaktive Einbindung von Drohnen, IoT-Sensoren, Kameras und anderen neuen Technologien intelligenter zu machen, und in diesem Experiment haben wir uns der Herausforderung der Automatisierung der Anlagenprozesssteuerung mit Hilfe von KI-Steuerungstechnologie gestellt. Wir haben nachgewiesen, dass KI in der Lage ist, Prozesse, die zuvor manuell auf der Grundlage der Erfahrung der Bediener durchgeführt wurden, autonom zu steuern, und wir sind fest von der Nützlichkeit und dem Zukunftspotenzial der KI-Steuerung überzeugt. Von den Anwendern haben wir gehört, dass sich nicht nur die Belastung der Bediener verringert hat, sondern dass allein die Tatsache, dass wir uns der Herausforderung dieser neuen Technologie gestellt haben und erfolgreich waren, eine Motivation ist, DX in die Zukunft zu führen. In Zukunft werden wir den mit KI gesteuerten Betrieb ausweiten und daran arbeiten, die Sicherheit, Stabilität und Wettbewerbsfähigkeit von Chemieanlagen zu verbessern.“
Takamitsu Matsubara, außerordentlicher Professor am NAIST:
„Ich bin hocherfreut zu hören, dass dieser Praxistest erfolgreich war. Bei der Arbeit von Chemieanlagen werden jetzt Datenanalysen und maschinelles Lernen genutzt. Die Technologien, die für autonome Kontrollen und die Optimierung von Tätigkeiten genutzt werden können, sind bis jetzt jedoch noch nicht vollständig ausgereift. Der FKDPP-Algorithmus für KI mit bestärkendem Lernen wurde 2018 gemeinsam von Yokogawa und NAIST entwickelt, um die autonome Steuerung von Chemiewerken zu ermöglichen. Obwohl die KI auf eine große Anzahl von Sensoren und Steuerventilen zurückgreifen muss, kann sie in einer begrenzten Anzahl von Lernversuchen eine robuste Kontrollstrategie entwickeln. Diese Funktionen haben zur Verbesserung der Effizienz des Entwicklungsprozesses beigetragen und während des Praxistests zur Realisierung einer autonomen Steuerung während des langen Zeitraums von 840 Stunden geführt. Ich denke, diese sehr schwierige Realisierung einer autonomen Steuerung in einer realen Destillationskolonne sowie die Tatsache, dass der Grad der praktischen Anwendbarkeit soweit gesteigert werden konnte, dass das gesamte Produktionsverfahren und die Sicherheit in ein einziges System integriert sind, sind für die gesamte Branche von hoher Bedeutung. Ich freue mich darauf zu sehen, wie es mit dieser Technologie weitergeht.“
Kenji Hasegawa, Vice President von Yokogawa Electric und Leiter der Yokogawa Products Headquarters:
„Der Erfolg dieses Praxistests rührte aus der Kombination der umfassenden Kenntnisse des Produktionsverfahrens und der operativen Aspekte, die nur die Kundschaft bieten kann, sowie aus der Stärke von Yokogawa bei der Nutzung von Messungen, Steuerung und Informationen für die Schaffung von Wert. Dies legt nahe, dass eine KI für autonome Steuerung (FKDPP) in signifikanter Weise zur Autonomisierung der Produktion, zur Maximierung der Rendite und zur ökologischen Nachhaltigkeit weltweit beitragen kann. Yokogawa ist weltweit führend bei der Entwicklung dezentraler Steuerungssysteme, mit denen der Betrieb von Produktionsanlagen kontrolliert und überwacht werden kann, und hat bereits das Wachstum verschiedenster Branchen unterstützt. Wir blicken fest auf die Welt des autonomen Betriebs, die das Modell für die Zukunft ganzer Branchen darstellt, und fördern so jetzt das Konzept IA2IA – „Industrial Automation to Industrial Autonomy“. Um eine starke und flexible Produktion zu realisieren, bei der der Einfluss von Unterschieden zwischen Menschen, Maschinen, Materialien und Methoden (den ʻ4 Msʼ) in den Branchen Energie, Werkstoffe, Pharma und vielen anderen Branchen mit berücksichtigt wird, werden wir die gemeinsame Entwicklung von KI für autonome Steuerungen zusammen mit unserer Kundschaft auf der ganzen Welt beschleunigen.“
1 Auf Grundlage einer von Yokogawa Electric im Februar 2022 durchgeführten Umfrage zu KI für direkte Veränderungen der Stellgröße in der chemischen Anlage.
2 Proportional-Integral-Derivative Kontrolle. Dies wurde erstmals 1922 von Nicolas Minorsky vorgeschlagen. Es handelt sich um eine Technologie zur Steuerung der Infrastruktur in der verarbeitenden Industrie, die zur Kontrolle von Faktoren wie Menge, Temperatur, Füllstand, Druck und Inhaltsstoffen eingesetzt wird. Damit erfolgt eine Steuerung in Richtung eines Zielwerts, wobei die Ergebnisse der einzelnen P-, I- und D-Berechnungen jeweils entsprechend der Abweichung zwischen dem aktuellen Wert und dem Sollwert verwendet werden. Bei dieser Art der Kontrolle treten Probleme auf: etwa eine Unmöglichkeit, multiple äußere Störungen (Wetter, Klima, Änderungen der Materialbeschaffenheit) sowie häufige Änderungen von Zielwerten zu bewältigen. Daher werden manuelle Kontrollen nötig.
3 Erweiterte Prozesssteuerung. Dabei wird ein mathematisches Modell genutzt, mit dem Prozessantworten prognostiziert werden können und über das dem PID-Regelkreis in Echtzeit Sollwerte vorgegeben werden, womit Produktivität, Qualität und Steuerbarkeit erhöht werden. Es lässt sich zudem leicht auf Kontrollen zum Zweck von Produktionserhöhungen, der Verkürzung der Arbeitszeit und dem Einsparen von Energie anwenden. Die Integration von APC führt zu geringeren Datenabweichungen. So wird es möglich, sich den Grenzen der Betriebsleistung zu nähern (d. h. dem Zustand, in dem die optimale Leistung erzielt werden kann). Dabei wirkt jedoch die Tatsache einschränkend, dass APC nicht in der Lage ist, auf die schnelle Verdampfung von Flüssigkeiten und ähnliche chemische Reaktionen, größere Veränderungen der Materialbeschaffenheit und Änderungen der Maschinen zu reagieren.
4 Die Menge des Zielstoffs, die durch den Veredelungsprozess tatsächlich aus Rohstoffen gewonnen wird
5 Das integrierte Steuersystem CENTUM VP ermöglicht es, dass das gesamte Produktionsverfahren weiterläuft, während Druck, Durchflussmengen, Temperaturen und ähnliche Faktoren überwacht und kontrolliert werden; zudem sind verschiedene Verriegelungsfunktionen für einen sicheren, stabilen Betrieb und zur Vermeidung von Unfällen integriert. Um Unfälle in Anlagen zu vermeiden, ist die Zusammenarbeit mit sicherheitstechnischen Systemen (SIS), Notabschaltungen (ESD), Brandschutzsystemen (F&G) usw. möglich.
6 Ein Mechanismus, der den Start verhindert, wenn bestimmte Bedingungen vor dem Betrieb nicht erfüllt sind. Damit wird die Sicherheit erhöht, indem fehlerhafte Vorgänge, Verfahrensfehler usw. vermieden werden.
7 Factorial Kernel Dynamic Policy Programming for Vinyl Acetate Monomer Plant Model Control, August 2018. https://ieeexplore.ieee.org/… IEEE (Institute of Electrical and Electronics Engineers). Das IEEE ist eine in den USA ansässige Organisation für akademische Forschung und technische Normung, die ihren Schwerpunkt in den Bereichen Elektro- und Informationstechnik hat. Es hat mehr als 400.000 Mitglieder in 160 Ländern auf der ganzen Welt.
8 Ein Niveauregelungssystem mit drei Behältern, das zur Durchführung von Übungen und Experimenten verwendet wird, bei denen der Wasserdurchfluss von einem Niveau zum nächsten geregelt wird. Dabei besteht das allgemeine Ziel darin, den Wasserstand auf der niedrigsten Stufe zu kontrollieren. Dazu zählen auch Geräte zur künstlichen Erzeugung von Störungen, die den Wasserfluss zufällig verändern. Aufgrund der Beschaffenheit von Flüssigkeiten ist die Kontrolle der Durchflussmengen eine schwierige Herausforderung in der verarbeitenden Industrie. Die Möglichkeit, solche Kontrollen durchzuführen, resultiert in erhöhter Produktivität an den Fertigungsstätten.
9 Scalable Reinforcement Learning for Plant-wide Control of Vinyl Acetate Monomer Process, Control Engineering Practice, Band 97, April 2020 https://www.sciencedirect.com/…
10 Yokogawa definiert KI für autonome Steuerung als KI, die selbständig die optimale Steuermethode ableitet und einen hohen Grad an Robustheit hat, sodass damit in einem gewissen Maß Situationen autonom bewältigt werden können, denen die KI bisher nicht begegnet ist.
Über die JSR Corporation
Die JSR Corporation ist ein multinationales Unternehmen, das weltweit mehr als 9.000 Mitarbeitende beschäftigt und ein führender Materiallieferant in einer Vielzahl von technologieorientierten Märkten ist. Das globale Netzwerk von JSR hat seinen Hauptsitz in Tokio (Japan) und verfügt über Fabriken und Büros in Europa, den USA, China, Taiwan, Südkorea und Thailand. JSR ist eine forschungsorientierte Organisation, die enge Zusammenarbeit mit führenden Innovationsträgern in einer Reihe von Branchen anstrebt, die einen wichtigen Beitrag zum gegenwärtigen und zukünftigen Wohlergehen der menschlichen Gesellschaft leisten: Biowissenschaften, elektronische Materialien, Displays, Kunststoffe und synthetische Kautschuke. Weitere Informationen über die JSR Corporation finden Sie auf https://www.jsr.co.jp/jsr_e/
Yokogawa bietet fortschrittliche Lösungen im Bereich der Mess-, Steuerungs- und Informationstechnik für Kunden aus verschiedensten Branchen wie z.B. der Energieindustrie, der chemischen Industrie, der Pharmaindustrie und der Lebensmittelindustrie. Das Unternehmen unterstützt seine Kunden bei der Bewältigung der immer komplexer werdenden Aufgaben in der Produktion, im Betriebsmanagement und bei der Optimierung von Anlagen, Energieverbrauch und Lieferketten mit digital gestützter intelligenter Fertigung, die den Übergang zu autonomen Abläufen ermöglicht.
Yokogawa wurde 1915 in Tokio gegründet und engagiert sich mit mehr als 17.500 Mitarbeitern in einem globalen Netzwerk von 119 Unternehmen an Standorten in 61 Ländern für eine nachhaltigere Gesellschaft. Etwa 200 Mitarbeiter der europäischen Yokogawa-Organisation sind an verschiedenen Produktions- und Vertriebsstandorten in Deutschland und am Sitz der Yokogawa Deutschland GmbH in Ratingen beschäftigt; rund 80 Automatisierungs-, Elektrotechnik- und Verfahrensingenieure arbeiten bei Yokogawa Deutschland an der Konzeption, Planung und Umsetzung von Automatisierungslösungen. In Europa besitzt Yokogawa einen eigenen Vertrieb sowie eigene Service- und Engineering-Organisationen. Yokogawa Europe B.V. wurde 1982 als Zentrale für Europa in Amersfoort, NL, gegründet.
Weitere Informationen zu Yokogawa finden Sie unter https://www.yokogawa.com/de/.
Yokogawa Deutschland GmbH
Broichhofstr. 7-11
40880 Ratingen
Telefon: +49 (2102) 4983-0
Telefax: +49 (2102) 4983-22
http://www.yokogawa.com/de
Telefon: +49 (2102) 4983-134
E-Mail: chantal.guerrero@de.yokogawa.com